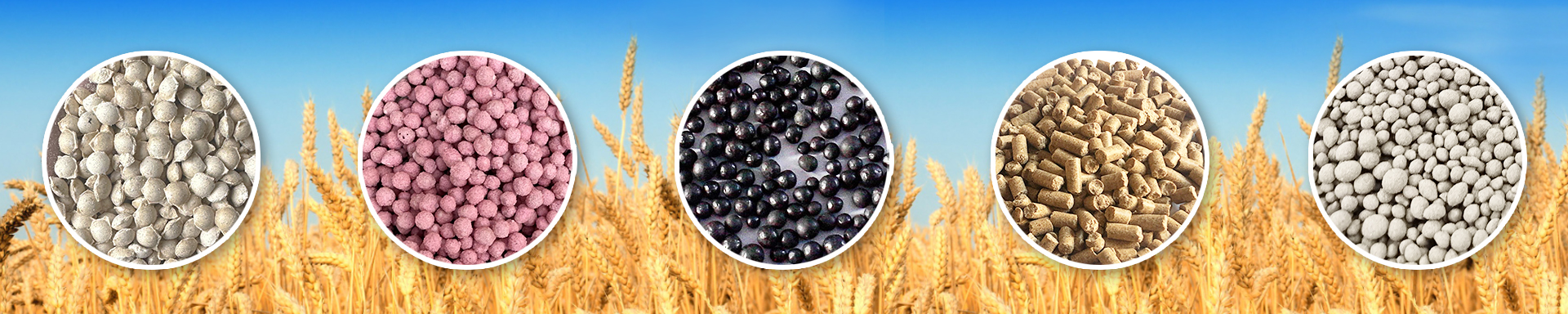
Rotary Drying and Cooling Machine
- Information
Introduction of Rotary Drying and Cooling Machine
The rotary dryer can dry or cool materials with high humidity. Widely used in agriculture, chemical industry, metallurgy, building materials, mining, food and other industries. It realizes the heat treatment and cooling process of materials through the rotation of the rotary drum and the circulation of hot air. It is often used for the treatment of fertilizer particles. The temperature at the bottom of the dryer can reach 400℃-800℃, and the hot air generated by the lower hot air furnace fully contacts the fertilizer particles, causing the water to continuously evaporate. During cooling, the granular fertilizer is continuously lifted by the lifting plate installed on the inner wall, and the suction of the internally induced draft fan accelerates the airflow inside the cylinder to achieve the purpose of uniform cooling. The treated materials can improve the quality and stability, enhance the hardness of the materials, and prevent the materials from deteriorating or agglomerating during transportation and storage.
Feature of Rotary Drying and Cooling Machine
1. High efficiency and energy saving: It adopts a rotary drum design to quickly dry and cool materials, and can make full use of energy to achieve high efficiency and energy saving.
2. Uniform drying/cooling: Through continuous rotation, the materials are evenly exposed to hot or cold air to avoid local overheating or overcooling problems.
3. Large production capacity: It can handle a large amount of materials and meet various production needs.
4. Multi-function: suitable for various types of materials, including granular, powdery, lumpy, and materials with different humidity.
5. Adjustability: The structure is simple and easy to operate, and staff can easily control the equipment and adjust parameters.
Working Process of Rotary Drying and Cooling Machine
The rotary drying and cooling machine fully exposes the materials to hot or cold air through the rotation of the rotary drum, thereby achieving the purpose of drying and cooling.
The material is put into the drum through the feeding device, and the other port is connected to the hot air or cold air device. When working, the drum begins to rotate continuously, driving the material to move. The hot air contacts the material evenly and takes away the moisture in the material for drying. After the work is completed, the cold air enters the rotary drum, contacts the material, and absorbs the heat energy of the material to achieve the purpose of cooling. The processed materials are discharged through the discharge port.
Technical Parameter of Rotary Drying and Cooling Machine
Rotary dryer | |||||||
Model | Cylinder | Production capacity | Inlet hot air temperature(℃) | Outlet hot air temperature(℃) | |||
Inside diameter(mm) | Length(mm) | Inclination(°) | Speed(r/min) | ||||
ZG12120 | 1200 | 12000 | 2-5 | 4.7 | 2-2.5 | 150-250 | 60-80 |
ZG15120 | 1500 | 12000 | 2-5 | 5.0 | 4-6 | 150-250 | 60-80 |
ZG15150 | 1500 | 15000 | 2-5 | 5.0 | 5-7 | 150-250 | 60-80 |
ZG18150 | 1800 | 15000 | 2-5 | 3.9 | 7-10 | 150-250 | 60-80 |
ZG20200 | 2000 | 20000 | 2-5 | 3.9 | 8-14 | 150-250 | 60-80 |
ZG22220 | 2200 | 22000 | 2-5 | 3.2 | 12-16 | 150-250 | 60-80 |
ZG24240 | 2200 | 24000 | 2-5 | 3.0 | 14-19 | 150-250 | 60-80 |
Rotary cooler | |||||||
Model | Cylinder | Feed temperature(℃) | Discharge temperature(℃) | ||||
Inside diameter(mm) | Length(mm) | Inclination(°) | Speed(r/min) | ||||
LQ10100 | 1000 | 10000 | 2-5 | 4.6 | 60-80 | <40 | |
LQ12120 | 1200 | 12000 | 2-5 | 4.6 | 60-80 | <40 | |
LQ15120 | 1500 | 12000 | 2-5 | 5 | 60-80 | <40 | |
LQ15150 | 1500 | 15000 | 2-5 | 5 | 60-80 | <40 | |
LQ18160 | 1800 | 16000 | 2-5 | 5 | 60-80 | <40 | |
LQ20200 | 2000 | 20000 | 2-5 | 60-80 | <40 |
Product Details of Rotary Drying and Cooling Machine
Dust removal equipment
The dust or particulate materials generated during the drying process may cause environmental pollution, equipment failure or health problems for workers. Therefore, dust removal is usually required before the drying operation to reduce the dust particles suspended in the air and ensure a clean and safe production environment.
At the same time, too much dust or particulate materials may affect the normal operation of the drying equipment, reduce the drying efficiency, and even affect the quality of the product.