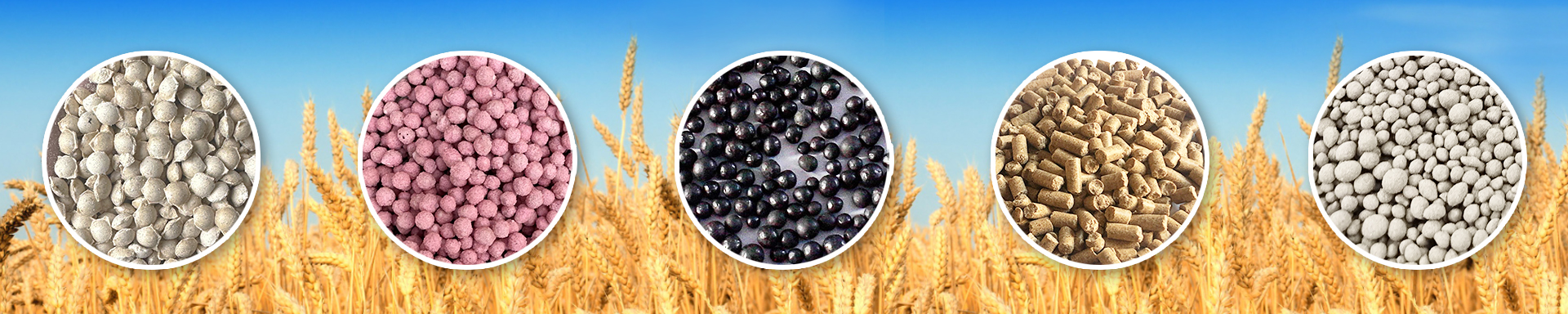
How to choose the right granulation process
2024-08-28At present, the commonly used granulation methods are agglomeration granulation, extrusion granulation, rotation granulation, spray granulation, etc. Due to different granulation methods, the finished granules after granulation have different properties.
Common granulation methods and their characteristics
Granulation method | Manufacturing condition | Physical properties of the product | ||||
Dry moisture /% | Drying temperature /℃ | Shape | Granularity | Disintegration in water | Manufacturing overhead | |
Spray drying process | 40~50 | >100 | Spherical | 0.1~0.5 | Quic | High |
Disc granulation proces | 10~15 | 50~80 | Roughly spherical | 0.2~3.0 | Middle | Low |
Extrusion method | 10~15 | 50~80 | Cylinder | 0.7~1.0 | Slow | Medium to high |
Agglomeration method | 10~15 | 50~80 | Amorphous | 0.1~2.0 | Middle | Medium to high |
Granulators for sale
▶ Disc granulator - wet granulation
The wet pan granulation process is adopted, and the ball formation rate is as high as 95%. It is mostly used for the production of organic fertilizer granules, and can also be used to produce bentonite cat litter, laundry detergent, dryer, fragrance beads, and other spherical granular materials.
▶ Double roller extrusion granulator - dry granulation
The extrusion granulation process is adopted, which is suitable for granulation of dry powdered materials. It is mostly used in compound fertilizer production and can form oblate particles at one time with high efficiency. In addition to powders such as urea, nitrogen, phosphorus potassium, and monoammonium phosphate, it can also be used to produce cat litter particles, graphite particles, etc.
▶ Drum granulator - steam granulation
The drum granulator can be equipped with a spray wet granulation method, which drives the material to grow by rolling. It is suitable for the granulation of high, medium and low concentration compound fertilizers, as well as medium and large-scale production needs.
Factors affecting the granulation scheme
Granulation is a process affected by many factors. It is necessary to clarify the granulation problem to be solved and the indicators that the product is expected to achieve, and then compare the capabilities and characteristics of various granulation processes.
The factors that need to be considered are mainly the following aspects:
1. Raw material factors
Different granulation methods are selected according to the characteristics of different raw materials. The fineness, moisture, and fusion of the material are all considered factors.
2. Product requirements
The particle size of the products obtained by different granulation methods is very different, such as spherical particles, oblate particles, irregular spherical particles, etc.
3. Other factors
Different granulation methods have different outputs and floor space. Therefore, it is necessary to consider the investment and processing costs of equipment and civil engineering. Dry granulation will inevitably cause dust. Wet granulation requires drying after granulation, which consumes energy. These are all things that need to be considered in the design of granulation process.
4. Drying method
Usually, wet granulation requires drying. There are many ways to dry particles, and drying equipment can be divided into two categories.
The drum dryer is a dynamic dryer that can achieve continuous discharge. The box-type cooler is in a static motion state and discharges materials in batches. Continuous drying equipment is mainly suitable for large-tonnage single varieties. For small and medium-sized production and multi-variety production, intermittent drying equipment is more appropriate.